Offer
CNC milling
CNC milling is one of the two basic and most commonly used machining methods. It consists in removing excess material from the surface with the use of specialized, carefully selected cutting tools. It is their type that determines the final results of the machining. The technique of metal milling was known as early as the 12th century, but the first complex machine for such machining was built in 1818 by the American engineer Eli Whitney. The first electronically controlled automatic machine was constructed in 1953.
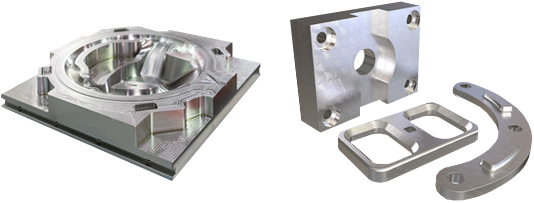
ADVANTAGES OF MACHINING ON CNC MILLING MACHINES
Currently, metal milling is performed with the use of modern, technologically advanced numerically controlled machines. They primarily guarantee:
• short production time of a single element,
• very high accuracy of model reproduction,
• precision of work in terms of fractions of a millimeter,
• very high repeatability thanks to the possibility of using the same machine settings for the production of hundreds of elements,
• elimination of human errors,
• reduction of material losses, and as a result – also the production costs of a single detail.
Conventional turning
A type of machining most often used to work on the external and internal surfaces of objects in the shape of rotating solids. It is also possible to obtain shapes other than rotating by turning. Turning involves separating a layer of material from an object with a turning knife in order to obtain the desired shape and dimensions. A lathe is a machine tool designed for external (turning) and internal (boring) surface machining. The basic movements are: the main rotary movement of the workpiece and the rectilinear feed movement of the tool.
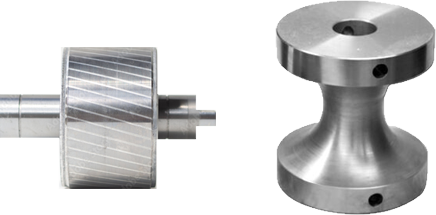
Grinding
Grinding is a type of mechanical processing that finishes a detail, it is carried out by abrasive machining, in which the cutting tool performs a rotary or sliding, rectilinear movement. Grinding can be done on holes, rollers and planes. The purpose of grinding is to protect and make the treated surface smooth. During the grinding process, a large amount of heat is released, which affects the physical properties of the material being ground.
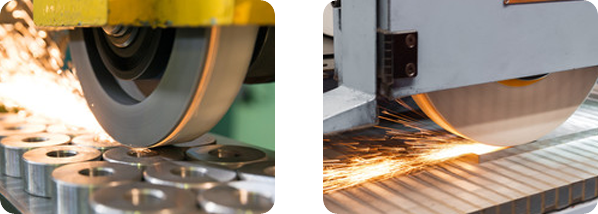
Drilling, Threading
Our offer includes a wide range of works in the field of professional machining. We perform, among others: drilling, reaming, boring, tapping, deepening. We use modern equipment for all works, thanks to which we can guarantee our customers not only high quality of machining works, but above all high repeatability of the process. This allows us to carry out orders regardless of the size of the circulation.
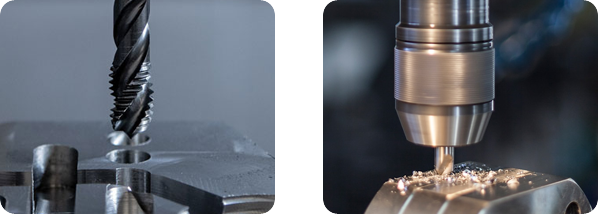
Additional services
Anodizing
Anodizing is mainly used for aluminum and its alloys, but can also be used for some types of steel, titanium and magnesium alloys.
Anodizing is used for three purposes:
– for anti-corrosive and mechanical protection of metal surfaces
– for decorative purposes – anodized aluminum alloys obtain a characteristic texture, and by adding coloring substances, colored coatings can be obtained.
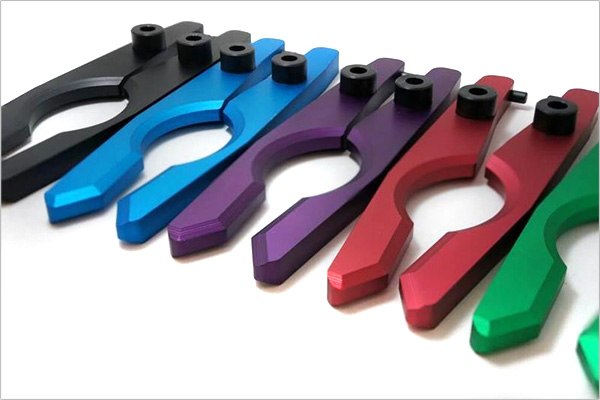
Hardening
Hardening processes are used to impart special mechanical properties to components in order to ensure that they are fit for their intended use.
Hardening is a type of heat treatment of a material consisting in heating a given material to an appropriate temperature called the hardening temperature, holding it at this temperature for the time necessary to rebuild the internal structure of the material (mainly phase changes) and then cooling it down quickly.
After such a treatment, local stress concentrations appear in the material, usually resulting in an increase in the strength properties: hardness, strength, yield point and elasticity as well as abrasion resistance at the expense of an increase in brittleness and a decrease in plasticity and elongation.
Moreover, we perform vacuum, gas and plasma hardening.
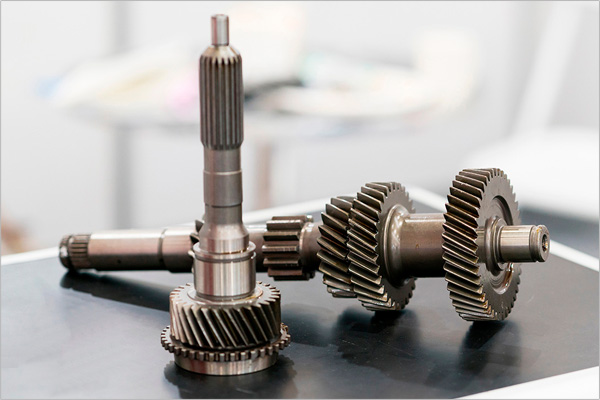
Galvanic treatment
Galvanization can be applied to a wide variety of surfaces, from most metals and alloys to selected plastics.
Galvanic coatings are used because they give the surface the expected technological, visual and protective parameters. Technical coatings perfectly protect the element during processing, increasing its corrosion and mechanical resistance, e.g. to impact and abrasion.
The most frequently used galvanic treatments by our customers are galvanizing and nickel plating.
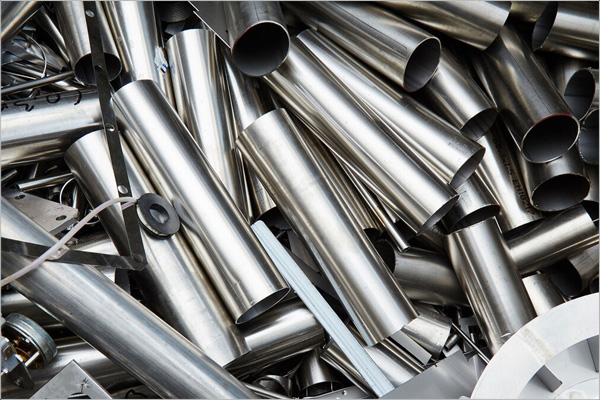
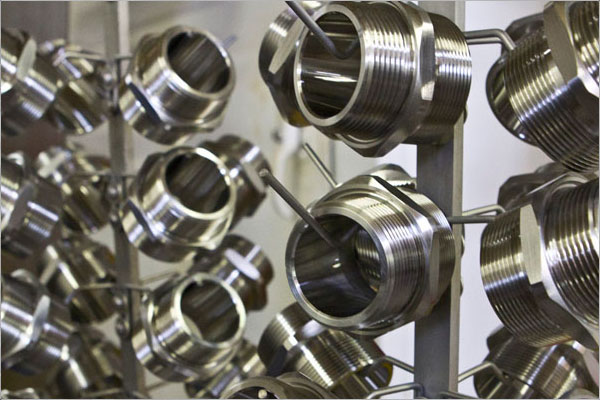
Blackening
To obtain a black, uniform matt coating, the steel is etched with acids or other chemical agents. This process is called oxidation. There are several methods of oxidation, mainly cold and hot oxidation. Ready-made oxides and preparations for blackening steel and other metals can also be used. The advantage of such measures is an appropriately selected composition, selected for a specific type of steel.
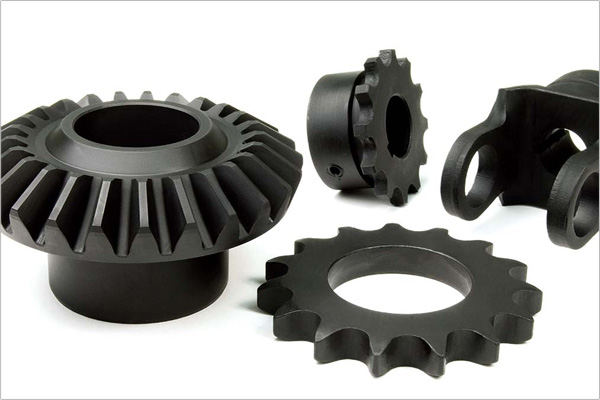
Contact
FREZO-TECH Kamil Najuch
Dobrynin 89
39-322 Rzemień
Poland
NIP: 817 218 93 58
REGON: 380 987 463
782 379 224
Work hours:
• Monday – Friday: 7:00 am – 11:00 pm
• Saturday: 7:00 am – 1:00 pm
• Sunday: closed
Contact
FREZO-TECH Kamil Najuch
Dobrynin 89
39-322 Rzemień
Poland
NIP: 817 218 93 58
REGON: 380 987 463
782 379 224
- Work hours:
• Monday – Friday: 7:00 am – 11:00 pm
• Saturday: 7:00 am – 1:00 pm
• Sunday: closed